by Dean E. Craft, principal, ISE Logik Industries
As appeared in the May 5, 2021 issue of “The Construction Specifier” magazine.
Often referred to as substrate “porosity”, substrate surface water absorptivity refers to the ability of a flooring substrate surface to absorb liquid relatively quickly. To better conceptualize, imagine a concrete masonry unit (CMU) block. If you were to place a drop of water on that CMU, the water would absorb very quickly into the block. Now, imagine a hard, smooth surface such as steel, or existing resilient flooring, or power-troweled concrete; all of which could serve as the substrate for many different flooring products. If you were to place a drop of water on any one of those surfaces, that drop of water would basically sit there and likely evaporate before ever being absorbed.
Historical context
Why is this of concern for a successful flooring installation? Before we attempt to address this question, it is helpful to provide some historical context. If we go back in time several decades, beginning in the 1970s and gaining significant momentum into and through the 1980s, there were growing concerns over indoor air quality; and, this eventually encompassed the flooring industry:
“On January 11, 1990, the National Federation of Federal Employees (NFFE), Local 2050, petitioned the EPA under section 21 of the Toxic Substance Control Act (TSCA), 15 U.S.C. 2620 to initiate rulemaking proceedings…to reduce emissions from new carpets.” (Federal Register, April 14, 1990, p. 17404).
While the EPA “…decided not to initiate the specific rulemaking proceedings …”, the EPA did decide to “… initiate a series of actions designed to assess and, if necessary, reduce the public’s exposure to compounds which may off-gas from carpeting.” (Federal Register, April 14, 1990, p. 17404) Upon mutual agreement with the EPA, the Carpet and Rug Institute (CRI) voluntarily agreed to conduct total volatile organic (TVOC) emission testing on various materials, and reported the results to the EPA’s Office of Toxic Substances in the “Carpet Policy Dialogue Compendium Report” (Sept. 27, 1991; p. 296).
Following closely on the heels of the Compendium Report, “… CRI launched its Green Label (1992) program to test carpet, cushions and adhesives to help specifiers identify products with very low emissions of Volatile Organic Compounds (VOCs).” (Green Label Plus: A Higher Standard for Indoor Air Quality; 2020). This resulted in a fundamental, rapid, and fairly radical change in the formulation of many of the adhesives and other constituent components used for flooring.
New vs. old
There is a common belief that the “good glues” of times past were insensitive to concrete substrate moisture. That is actually not the case and there is literature going back to the 1950s discussing this topic. Building on that misconception, many believe that the “newer water-based” adhesives are the primary source of flooring installation issues. Historically speaking, those “newer” glues are not really that new anymore; many of which began their evolution almost 30 years ago. Further, over that time, there have been untold millions of square feet of very successful installations. However, there is a fundamental difference between many of those older adhesives and many of the newer ones; especially in how they behave once applied to a substrate surface.
From time to time, in response to changing technologies, new ASTM standards related to flooring installation are published that may go unnoticed across the specification community. One such ASTM, F3191 Standard Practice for Field Determination of Substrate Water Absorption (Porosity) for Substrates to Receive Resilient Flooring, attempts to proactively identify just how an adhesive should be applied, and even what adhesive should be specified.
Porous vs. non-porous
Today as in the past, the leading influencer of whether a new concrete surface is porous or non-porous is the applied concrete flatwork finishing techniques. Once the jobsite is ready for the concrete surface preparation and installation of floorcoverings, it is the floorcovering contractor’s responsibility to determine whether the concrete surface is porous or non-porous, and proceed with the correct methods and compatible products for the determined porosity. The coalescence of an impermeable floorcovering material and a non-porous concrete surface reduces moisture from coming in, but also from escaping. Using wet-set water-based adhesives necessitate water loss through evaporation and/or absorption for adhesive strength development, whereas a moisture-cured adhesive absorbs moisture from the air or substrate for strength development. Knowing whether the concrete surface is porous or non-porous prior to applying that adhesive, and enacting applicable installation methods, are crucial for a long-term successful floorcovering installation.
Determining factors of porosity
Let’s take a look at some of factors that determine the concrete surface porosity. During the concrete finishing stage, bleed water (referring to the process in which free water in the mix migrates upward to the surface, as the settlement of heavier solid particles such as cement and aggregates occurs) must be managed. One of the biggest factors in the bleed water rate is the water-to-cement ratio (the ratio between the weight of water and cement in the concrete mix and hereafter referred as w/cm ratio), and cement types and aggregates sizes can play a significant role in determining the rate. The concrete flatwork finisher seeks to effectively manage the bleed water to ensure the quality of the concrete. Bleeding of the free water continues until the cement paste has hardened enough to finish the sedimentation process. An increased w/cm ratio can result in excessive bleeding and increased capillary size and quantity. The aggregates and cement types used in the concrete also play a roll in bleed water; the less fines in the concrete mix, the greater degree of bleeding will occur.
In its fresh state, concrete is a suspension of solids in water. As compaction occurs, the solids (with a greater specific gravity than water) settle. This sedimentation displacement pushes the water upwards and the water will even appear on the surface as a layer. On windy days or when the temperatures are hot, the bleed water may not be as noticeable since the evaporation rate may be greater than the bleed rate. Longer initial set rates, as in when retarding admixtures are used, can increase bleeding. Homogeneity loss and permeability differences are the direct effects of concrete bleeding. Not all bleed water reaches the surface of the concrete, as some of the bleed water remains trapped under aggregates and reinforcement materials and does not rise to the surface. A negative effect of this may be a weakening of the bond between the cement paste and those materials.
The role of the contractor
A lot of responsibility rests on the shoulders of the concrete flatwork contractor, who is not there to eliminate the bleed water, but rather to manage it. The w/cm ratio of the concrete decreases as the free water migrates to the surface and evaporates, resulting in a decreased capillary porosity and an increased density – both desirable characteristics in most cases. To avoid working the free water back into the mix, it is important not to begin finishing operations before most of the bleed water has evaporated, which can result in an increase in permeability and increase the w/cm ratio again after it has been reduced. Finer blends of supplementary cementitious materials, such as fly ash and silica fume, can decrease bleed rates. Some fibers decrease bleed rates as they control the speed of migration of the free water to the surface while inhibiting the settling of solids.
Interior concrete slabs are predominantly troweled finished, with common finishing nomenclatures such as “hard troweled”, “machine troweled”, and “light steel troweled”, resulting in a reduction in surface air content and change in hardened air void parameters which provides a more dense and non-absorptive surface. When tested according to ASTM F3191-16 Standard Practice for Field Determination of Substrate Water Absorption (Porosity) for Substrates to Receive Resilient Flooring, the indication is often a non-porous surface. Air content of concrete reduces with the increase of cementitious fineness, and vibration step in finishing concrete. On average, three minutes of vibration decrease the air content by up to 50%. Add to that the troweled finish process, and the default new concrete finish for an interior slab is non-porous.
Finishing results that are done correctly result in a concrete surface that is serviceable for its required specified use. Once the concrete is leveled and the bleeding stops, all other finishing operations may proceed. Concrete curing is the process by which freshly placed concrete is maintained at suitable moisture and temperature conditions enabling hydration to proceed at an acceptable rate. Under such conditions in the beginning stages of the concrete’s life, it is protected from premature excessive evaporative moisture losses and temperature extremes which can negatively impact its strength and durability. The harmful effects of such major influencing factors, such as high wind velocity, ambient temperature, relative humidity and concrete temperatures, can all be controlled when a suitable environment is created through best methods and practices. A lack of proper curing may result in a more porous and weaker concrete microstructure, which allows easier and quicker access of agents into the concrete.
When the floorcovering contractor is on the jobsite and reviewing the concrete slab condition, a key crucial factor of accurately installing a flooring adhesive, cementitious underlayment, primer, and other similar products, is to know if the substrate’s surface is either porous or non-porous. Test procedure as directed in ASTM F3191-16 is simple and quick. Details of the testing conditions and how to conduct the test directly from the ASTM are:
7. Conditioning
7.1 Substrates should be at the service temperature and relative humidity expected during normal use or at the conditions required for installation of the floor covering material per the relevant manufacturer’s specifications. If this is not possible, then the substrate and ambient temperature shall be 75°F +/- 10°F (23.9 +/- 5.5 °C) and the ambient humidity shall be 50% +/- 10% relative humidity.
To meet these conditions, in most cases the interior space will need to be climate controlled for the test to proceed and produce accurate results. Especially in new construction, achieving and maintaining the proper climate-controlled environment is often neglected, even during the installation of floorcoverings. The step by step procedure of conducting the test is as follows:
8. Procedure
8.1 All substrates to receive resilient floor covering materials that require a determination regarding substrate absorption/ porosity shall be tested for surface water absorption prior to the installation of resilient flooring, adhesives, primers, self-leveling underlayments, and related products regardless of age or grade level.
8.2 The substrate surface shall be prepared in the exact manner as planned or as required for each specific floor covering material installation.
8.3 To test for field substrate water absorption at the substrate’s surface, place a single drop of potable water (approximately 0.05 mL) on the substrate surface using a pipette, water dropper, straw, etc., after the substrate surface has been prepared as described in 8.2.
TABLE 1 ASTM Practice for Substrate Water Absorption Rate
Length of Time to Absorb Substrate Determination
< 1 minute Porous/Absorptive > 1 minute Non-porous/Absorptive
So, a field test takes about one minute of time for determination if the concrete surface is porous or non-porous. Once identified, this will determine the best practices and methods to employ; as well as the correct choice of flooring adhesive, cementations underlayment, primer, and other similar products.
The condensation effect
A factor that is often overlooked but can be a conflicting variable when testing for concrete surface porosity is condensation. Commonly referred to as “sweating slab syndrome” or “concrete sweating”, this occurs when with the substrate surface temperature is at or below the dew point temperature of the ambient air above and the moisture vapor in the air converts to liquid and condenses on the concrete surface. Several environmental factors have a significant impact on the success of a floorcovering installation. Among the most important are ambient relative humidity and ambient temperature, substrate surface temperature, and dew point.
The climate controlled systems in place at a jobsite, what settings they are on for controlling ambient temperature and ambient humidity, whether continuous or non-continuous operation, the efficacy of those climate controlled systems, and air leakage into the building such as open areas for construction traffic, are all important factors in determining if the surface in question is at risk of developing condensation. Problems tend to occur when the substrate’s surface temperature matches the dew point temperature. This is more likely to happen late at night or early morning hours. In order to prevent the introduction of condensation during concrete surface porosity testing, avoid conducting the test unless the substrate is “surface dry”; with “surface dry” defined as the complete absence of any visible dampness, water, snow, ice (or other precipitation) on the substrate surface, and, with ambient conditions at least 5°F above dew point with the temperature rising.
The importance of surface prep
With existing concrete slabs that have been in use with floorcovering products applied, it is critical that the concrete surface is prepared and readied for accepting the new floorcovering product before the concrete porosity test is conducted. Existing adhesives, sealers, coatings, etc., that are to be removed before the new floorcovering products are applied, must all be removed before the test is conducted. Residuals after removal of existing applied products may decrease the porosity of the concrete surface to a non-porous surface. Mechanical removal of existing products is the preferred method, as many chemical type removers cannot be completely extracted from the concrete after the removal process and continue to do what they were designed to do – remove adhesive! Check for compatibility of residuals from old adhesives left on the concrete with the new flooring products to be installed, as there may be a requirement for isolation to prevent coagulation. This is typically resolved with an encapsulation membrane including cementitious products or liquid applied products.
An existing Concrete Surface Profile (CSP) may not be the profile that is required for the product to be installed. Thus, if the concrete surface is not prepared at the corresponding CSP for the product to be installed before the porosity test is conducted, the test results would not be commensurable with the concrete surface to receive the floorcovering product. For example, a concrete surface with no CSP will probably be less porous than with a CSP of 1. The Concrete Surface Profile numerical value is derived from the measurements of the average distance from the peaks of the surface to the valleys as seen through a cross-sectional view of the concrete surface. This can be referred to as amplitude – the maximum extent of the oscillation. The CSP standards numerical values are stated as 1 – 10, with 1 being the smoothest and 10 being the roughest. A concrete surface profile that is less than one would be identified as a surface with no identifiable CSP corresponding value, and is usually the result of a steel troweled finish.
Use of underlayment
If the flatness or levelness of the concrete surface requires improvement to bring within acceptable tolerances for the finished floorcovering, a cementitious underlayment may need to be applied. The test method for measuring the flatness and levelness of the concrete surface is ASTM E1155-20 Standard Test Method for Determining FF Floor Flatness and FL Floor Levelness Numbers. Many cementitious underlayments and floor levelers require a porous surface, or a CSP of 1 or more. Primers/bond promoters may also be required before applying the cementitious product and on top of the cementitious product. The direct way to address a concrete surface that indicates a non-porous test result, is to mechanically prepare the surface to render it porous and at the proper CSP for the product to be installed. If an alternative product is available for leveling the concrete surface that can be applied to a non-porous surface, then it should definitely be considered, as it would reduce labor and time costs for concrete surface preparation and minimize the production of silica dust on the jobsite.
Applying the adhesive
With a flooring adhesive, the correct method over a porous surface may be as simple as an application rate and open time difference vs. a non-porous surface, instead of a change in flooring adhesive product. Installation data sheets for flooring adhesives generally include a table or chart that recommends trowel size, application rate, and “open time” or “flash time” for both porous and non-porous surfaces. The working time of the adhesive may be reduced as the flash time increases, so the floorcovering installer will need to manage this time accordingly. The non-porous surface flash time of the adhesive is greater than the flash time for a porous surface (another 30 minutes for example) and is influenced by concrete surface temperature, ambient relative humidity and temperature, and air-flow. This is regardless of whether the adhesive is being applied over a porous or non-porous surface. This flash time facilitates the evaporation of moisture from the adhesive, and if not allowed a sufficient flash time, this moisture becomes trapped when installing an impermeable floorcovering. The result is that adhesive cure and strength development is compromised. What happens when this is compromised? The integrity of the floorcovering bond to the subfloor surface is jeopardized and adhesive migration may also develop between the seams and transition areas to the surface of the floorcovering.
The role of the architect
So, what about the specification input? As the author of the specifications that constitute part of the Contract Documents, the architect (and their consultants) has considerable impact on this issue. All too often, under which adhesive to use buried within various 09 Divisions, the phrase, “as recommended by flooring manufacturer” is embedded into the specs. Without many even being aware, that short phrase may significantly limit the options for addressing a non-porous substrate surface. As an example, the manufacturer of the specified flooring may not even offer an adhesive product for the specified floorcovering product that can be used over a non-porous surface. This recently occurred with a 200,000 f2 hospital addition in central Florida. The specified flooring manufacturer’s instructions “required” their branded adhesive to be used. Upon closer analysis, their adhesives were only for porous substrates. Their literature further stated that if the substrate was non-porous per ASTM F3191, the concrete substrate would need to be bead-blasted, then self-leveled, just so that their porous substrate only adhesive could be used. Upon discussion with the architect, that initial adhesive specification language was changed to “… an adhesive compatible with flooring material backing and suitable for substrate porosity/absorption conditions.” Seemingly a simple word change, but had that entire project required bead-blasting and self-leveling, the change order could have been on the magnitude of $500,000 to $750,000 and weeks of additional time. By thinking through the ramifications of the spec language in conjunction with the specified flooring, the design team was able to subtly alter the language, apply the principles of lean construction and sustainable design, and enable the construction team to stay on budget and schedule for their project flooring installation.
Success is achievable
If the flooring adhesive chosen for the project is not recommended over a non-porous surface, in most cases there are alternate flooring adhesive options available that are. And as a rule, check with the floorcovering manufacturer and adhesive manufacturer for compatibility of products. As long as the porosity of the concrete is determined, and the correct flooring installation products are used with the correct adhesive spread rate, and flash times are followed that are all harmonious with the concrete surface, there is no reason that flooring installations in both porous and non-porous concrete surface conditions cannot be successful.
For more information, contact Dean at [email protected]
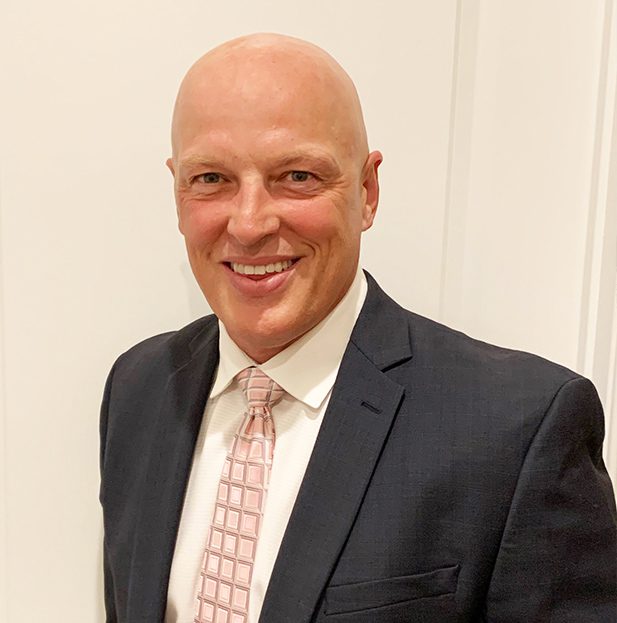
Dean E. Craft, DBA, CSI, CDT, CCCA, ASTM, ACI
Lt Col USMCR (ret.)
Principal of ISE Logik Industries, manufacturer of concrete moisture products, Director of the Southeast Region of CSI and President of the CSI Orlando Chapter, Dean has presented more than 1000 times on how to proactively address concrete moisture in the design phase. Dean is the principal author and technical chair of ASTM F3191 – 16: “Standard Practice for Field Determination of Substrate Water Absorption (Porosity) for Substrates to Receive Resilient Flooring”, completed his doctoral work in 2017 with a dissertation entitled “Fallacy of Current Industry Approach to Assessing Concrete Moisture Before Flooring Installation”, and is a voting or participating member of the ASTM Committee D08 on Roofing and Waterproofing, ASTM Committee F06 on Resilient Floor Coverings, American Concrete Institute, and National Ready-Mix Concrete Association Research, Engineering & Standards Committee. Dean is a retired, U.S. Marine Corps Lieutenant Colonel with 23-years of total service; and graduate of the United States Naval Academy (BS), the Naval Postgraduate School (MS), and California Intercontinental University (DBA; Doctorate in Global Leadership).