If it’s been a while since chemistry class, pH is “the quantitative measure of the acidity or basicity of a water (aqueous) or other liquid solution” (Britannica, 2020). The pH scale goes from 0 to 14 and along that scale, a pH of 7 is considered neutral, a pH of less than 7 indicates acidity, and a pH greater than 7 indicates basicity. Another important reminder is that the pH scale is logarithmic; meaning that an increase or decrease of a whole number value represents a tenfold change in concentration. For example, a pH of 3 is ten times more acidic than a pH of 4. Likewise, a pH of 3 is one hundred times more acidic than a pH of 5.
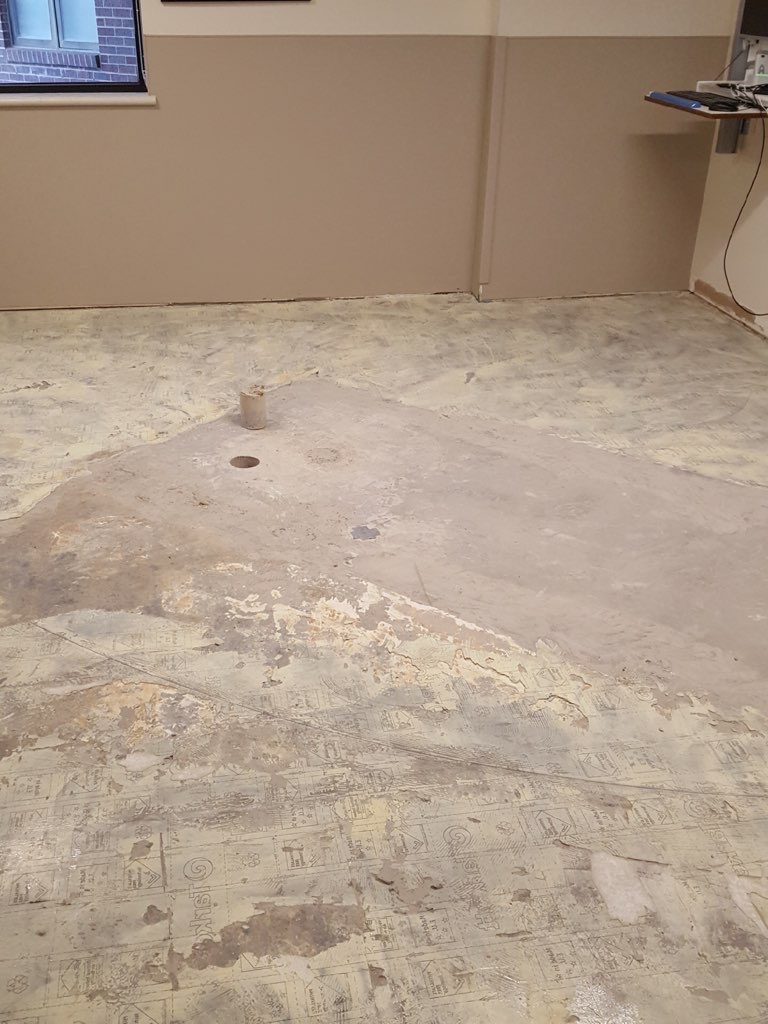
Why is this of concern for flooring installation?
Because concrete slabs are one of the most commonly encountered substrates that will receive flooring products; and, because some “floor adhesives on cement-based substrates may degrade if the pH is high enough and this has in many cases led to emissions of odorous substances, deteriorated indoor air quality” and failed flooring (Anderberg & Wadsö, 2008).
When concrete, or a cementitious underlayment, is still in its plastic, slurry form, it has a very high pH because as Portland cement hydrates, calcium hydroxide is formed. Dissolved calcium hydroxide produces an alkaline solution with a pH typically in the range of 12 to 13 (ASTM F710-21), more than strong enough to readily cause chemical burns. If you’ve ever gotten wet cement or wet cementitious underlayment on your hand and did not clean it off soon enough, you know just how caustic those materials can be.
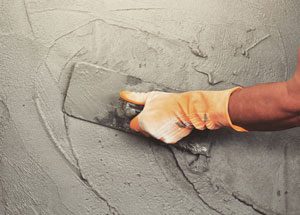
During concrete placement and consolidation, excess mix water migrates to the slab surface, typically resulting in a higher concentration of soluble alkalis in the surface region of the concrete slab. “As the uncovered surface of a concrete slab is exposed to atmospheric carbon dioxide, the surface pH is lowered to a range of pH 8 to 9 due to a natural process referred to as carbonation” (ASTM F710-21). This carbonated layer helps protect installed flooring. Therefore, so as long as any near-surface soluble alkalis remain dry, that is not “in solution”, it is very unlikely they will cause harm to installed flooring system components.
When a water-based adhesive is applied to the surface of a bare concrete slab there may be sufficient free water in the adhesive to place soluble alkalis in the surface region of the slab into solution and create a potentially damaging high pH situation beneath the installed flooring material. This elevated pH effect of water in an adhesive may be a short-term condition “if”: 1) the surface region of the slab is porous, and 2) and the relative humidity level in the slab is 85% or lower, as measured by Test Method F2170.
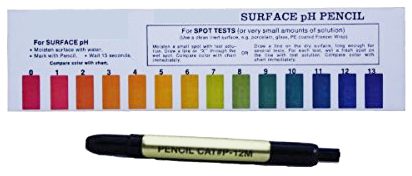
It is extremely important to understand that this discussion of pH is not solely about soluble alkalis possibly going back into solution; it is multi-faceted discussion of the type of adhesive in combination with substrate absorption/porosity. According to ACI PRC-302.1 (2015), interior concrete slabs that will receive flooring are usually finished by troweling in an effort to achieve the degree of “flatness” required by many flooring products (ASTM F710, 2021). The process of troweling produces “a dense, smooth, hard surface” (ACI PRC-302.1, 2015). So, not only does troweling help to achieve the required flatness, it also, in most cases, densifies the concrete substrate surface to what is referred to as a non-porous/non-absorptive substrate (ASTM F3191-16).
Fast forward to time of installation. Since most new concrete slabs are troweled, they are very likely going to test as non-porous/non-absorptive per ASTM F3191-16. This has recently been recognized within the latest version of ASTM F710-21 and substrate surface porosity testing is now required for all concrete slabs regardless of age or elevation that will receive resilient flooring. If this testing is not done, and the wrong type of adhesive or installation method is used on concrete with decreased ability to absorb the water from the adhesive, alkaline hydrolysis of the adhesive and subsequent debonding of the floor covering can readily occur (Plesser, 2007).
For the past 23 years there has been a pH procedure embedded and required within ASTM F710; that recently changed and within the most recent version of F710-21, the pH procedure no longer exists.
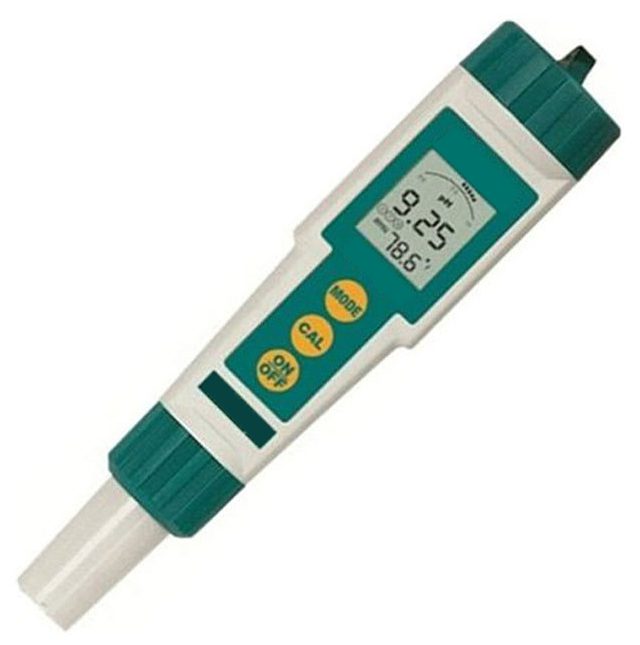
There is a new proposed pH Guide standard that is currently under balloting within the ASTM F06 Committee on Resilient Flooring. It has been in the works for the past five years and it is hoped that it will achieve consensus acceptance by the flooring industry by November of this year. Unfortunately, if the committee does not adopt the proposed pH Guide standard, no consensus reference method for pH will be available for manufacturers and project design teams to point to. The result could be that every flooring system component may have its own particular method to assess substrate surface pH.
For more information and insight on this important topic, listen to Dean Craft’s interview with Dave Foster on TalkFloor.com
As new developments and updates occur on pH testing, stay tuned!
References:
ACI PRC-302.1-15 Guide to Concrete Floor and Slab Construction. (2015). American Concrete Institute, 38800 Country Club Drive Farmington Hills, MI 48331, ww.concrete.org.
Anderberg, Anders & Wadsö, Lars. (2008). Degradation of floor adhesives as a function of pH. Polymer Degradation and Stability – POLYM DEGRAD STABIL. 93. 329-334. 10.1016/j.polymdegradstab.2007.12.007.
ASTM F710-21. (2021) Standard Practice for Preparing Concrete Floors to Receive Resilient Flooring, ASTM International, West Conshohocken, PA, 2021, www.astm.org.
ASTM F3191-16. (2016) Standard Practice for Field Determination of Substrate Water Absorption (Porosity) for Substrates to Receive Resilient Flooring, ASTM International, West Conshohocken, PA, 2021, www.astm.org.
Britannica, T. Editors of Encyclopaedia (2020, June 3). PH. Encyclopedia Britannica. https://www.britannica.com/science/pH.
Plesser, T. (2007). Moisture in Concrete – Alkaline sensitive surface treatments. SINTEF Building and Infrastructure. Oslo, Norway.
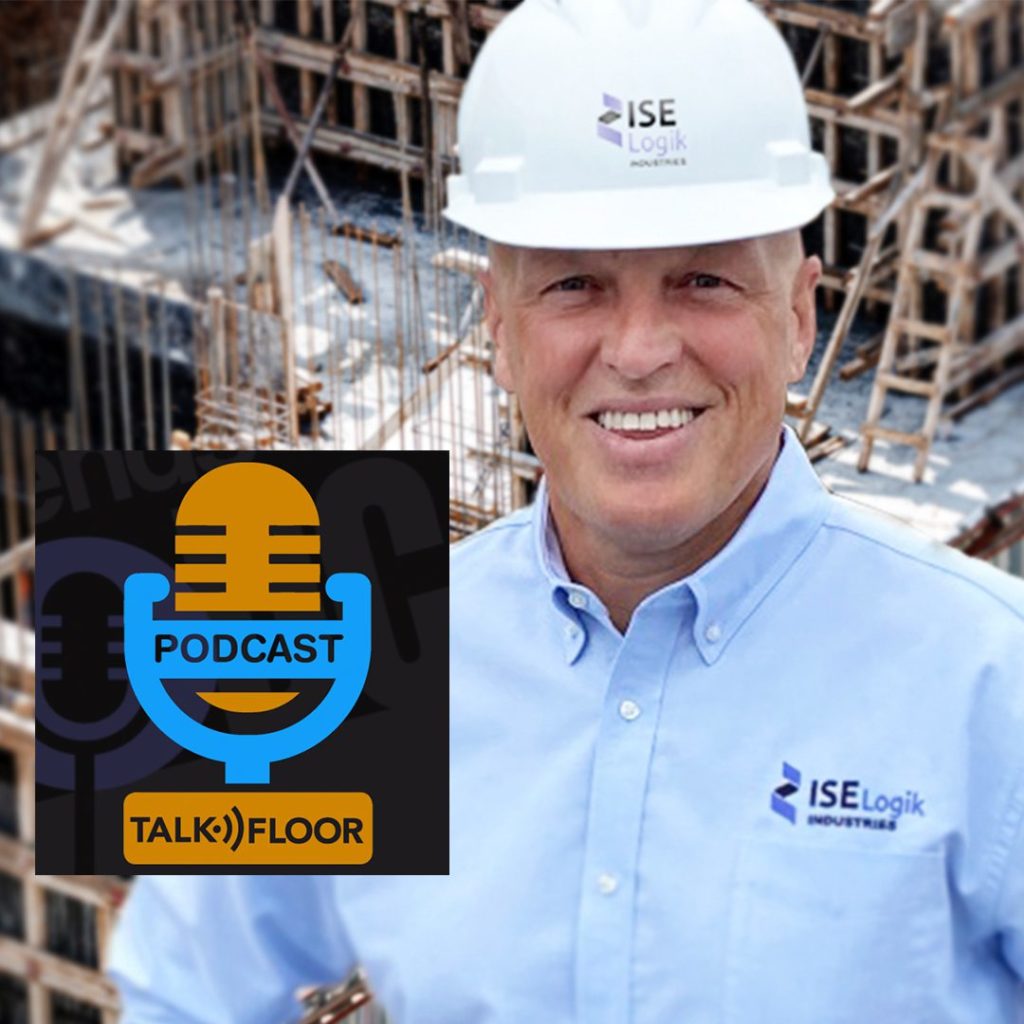
Dean E. Craft, DBA, CSI, CDT, CCCA, ASTM, ACI
Principal of ISE Logik Industries, manufacturer of concrete moisture products, Director of the Southeast Region of CSI and President of the CSI Orlando Chapter, Dean has presented more than 1000 times on how to proactively address concrete moisture in the design phase. Dean is the principal author and technical chair of ASTM F3191 – 16: “Standard Practice for Field Determination of Substrate Water Absorption (Porosity) for Substrates to Receive Resilient Flooring”, completed his doctoral work in 2017 with a dissertation entitled “Fallacy of Current Industry Approach to Assessing Concrete Moisture Before Flooring Installation”, and is a voting or participating member of the ASTM Committee D08 on Roofing and Waterproofing, ASTM Committee F06 on Resilient Floor Coverings, American Concrete Institute, and National Ready-Mix Concrete Association Research, Engineering & Standards Committee. Dean is a retired, U.S. Marine Corps Lieutenant Colonel with 23-years of total service; and graduate of the United States Naval Academy (BS), the Naval Postgraduate School (MS), and California Intercontinental University (DBA; Doctorate in Global Leadership).